Solderability
A destructive test and a common flow-down requirement performed to ensure that the solder will stick to the leads properly in next level assembly. A proper solder connection indicates proof of wetting and is a reliable and quantitative way to measure solderability.
How It Works
-
Method
Most common method is the “dip-and-look” test, where the component’s lead are dipped into a molten solder bath, and then visually inspected to assess the extent of solder coverage on the surface. -
Wetting balance analysis
A more precise method uses a wetting balance to measure the force exerted by the solder on the component’s surface as iit’s dipped, providing quantitative data on solderability. -
Flux application
Before dipping, a flux is often applied to the component’s leads to facilitate wetting by the solder. -
Inspection criteria
The results are evaluated based on factors like the amount of solder coverage, the uniformity of wetting, and the presence of any defects like dewetting or non-wetting areas. -
Destructive test
Solderability testing is usually considered destructive as the process can damage the component’s surface, so it’s often performed on a sample of components rather that the entire batch.
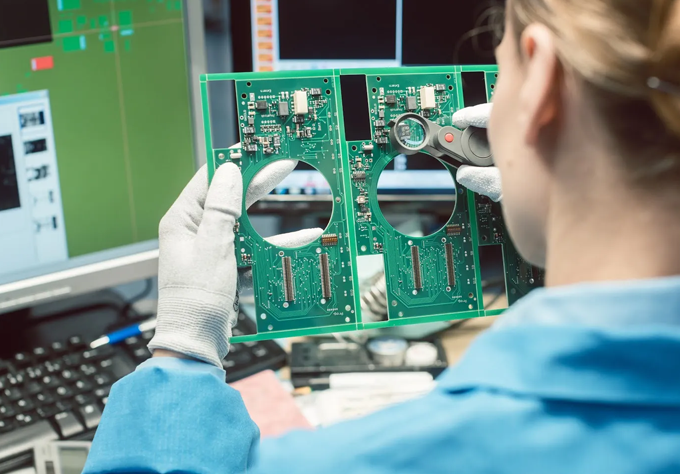